Armorthane Tech Tips: Troubleshooting Blister Issues in Coating Applications
Coating applications are a vital part of protecting surfaces from wear, environmental damage, and chemical exposure. Armorthane, a global leader in advanced protective coatings, provides top-tier solutions to ensure durability and reliability. However, even the best materials and practices can sometimes encounter challenges, with blistering being one of the most common issues.
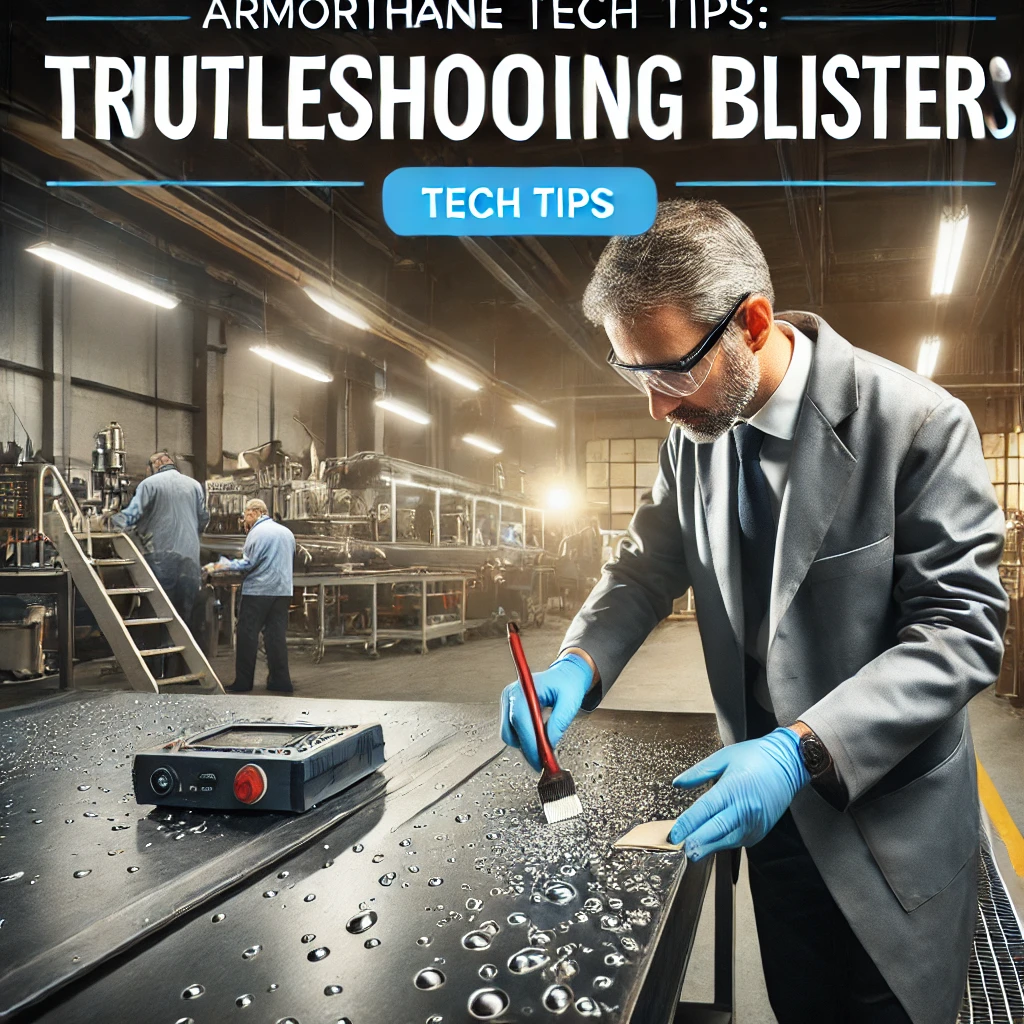
This comprehensive guide, part of the Armorthane Tech Tips: Troubleshooting Blister series, explores the root causes of blistering, solutions to fix the issue, and practical steps to prevent it in future projects. Whether you’re an experienced professional or a DIY enthusiast, these insights will help you achieve long-lasting, flawless results.
What Is Blistering in Coatings?
Blistering refers to the formation of raised bubbles or spots beneath a coating’s surface. These defects can range from minor cosmetic blemishes to severe issues that compromise the coating’s adhesion and protective properties.
Blistering typically occurs when air, moisture, or volatile substances are trapped beneath the coating during or after application. When exposed to environmental factors like heat or pressure, these trapped elements expand, creating blisters that weaken the coating.
If left unresolved, blistering can result in:
- Compromised Protection: Exposing the substrate to damage such as corrosion or wear.
- Increased Maintenance Costs: Repairs and reapplications can be costly and time-consuming.
- Diminished Appearance: Blistering can ruin the smooth, professional look of the coating.
Understanding how blistering happens is essential for implementing the right solutions. That’s why the Armorthane Tech Tips: Troubleshooting Blister guide is your go-to resource for addressing this challenge effectively.
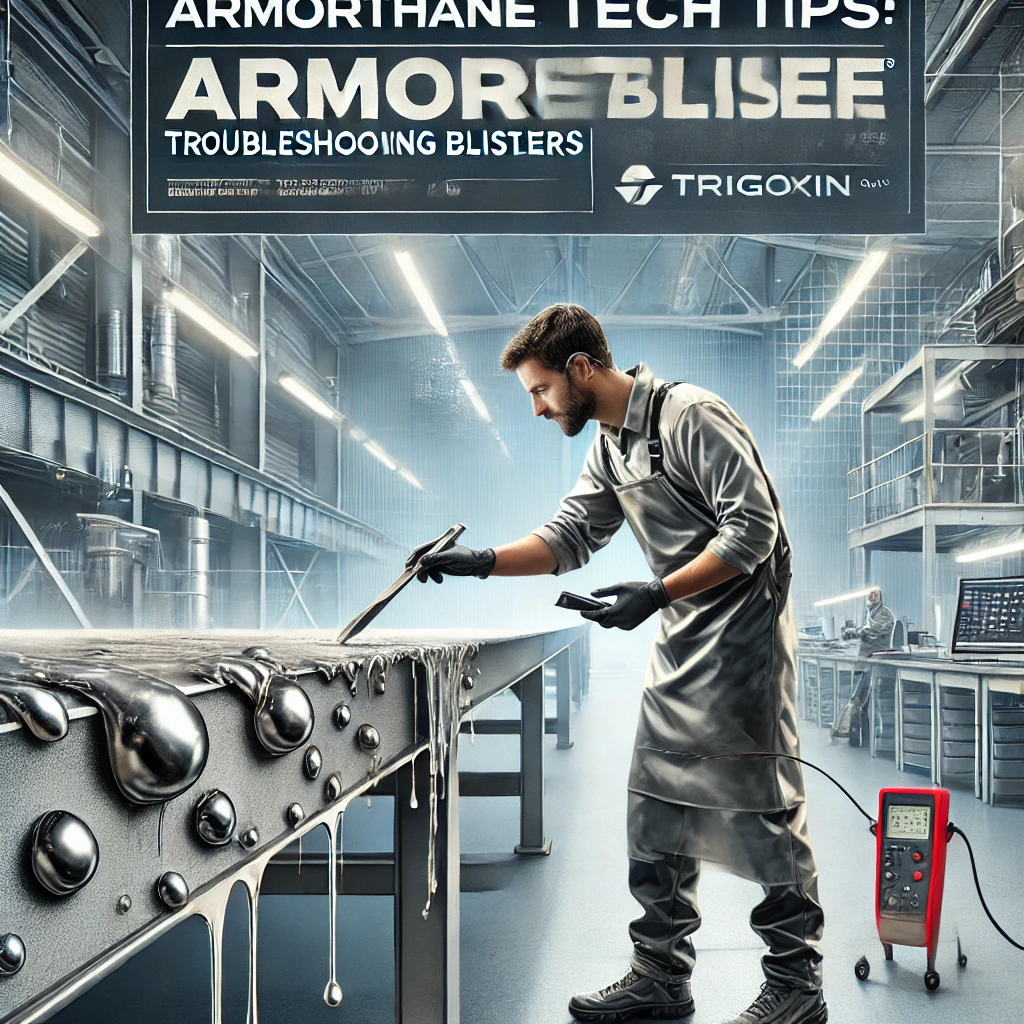
Common Causes of Blistering
Blistering can arise from several factors, often involving a mix of environmental, material, and procedural issues. Below, we explore the most common causes and provide actionable solutions.
1. Moisture in the Substrate
One of the primary reasons for blistering is moisture trapped in the substrate. When coatings are applied to damp surfaces, the moisture can evaporate during curing, creating pressure that results in blisters.
Where It Happens:
- Concrete substrates that retain moisture.
- Wood or porous surfaces exposed to water.
- Metal surfaces with condensation.
Prevention Tips:
- Use a moisture meter to ensure substrates are dry before application.
- Allow adequate drying time after cleaning or preparation.
- Apply a moisture-resistant primer, especially on porous surfaces.
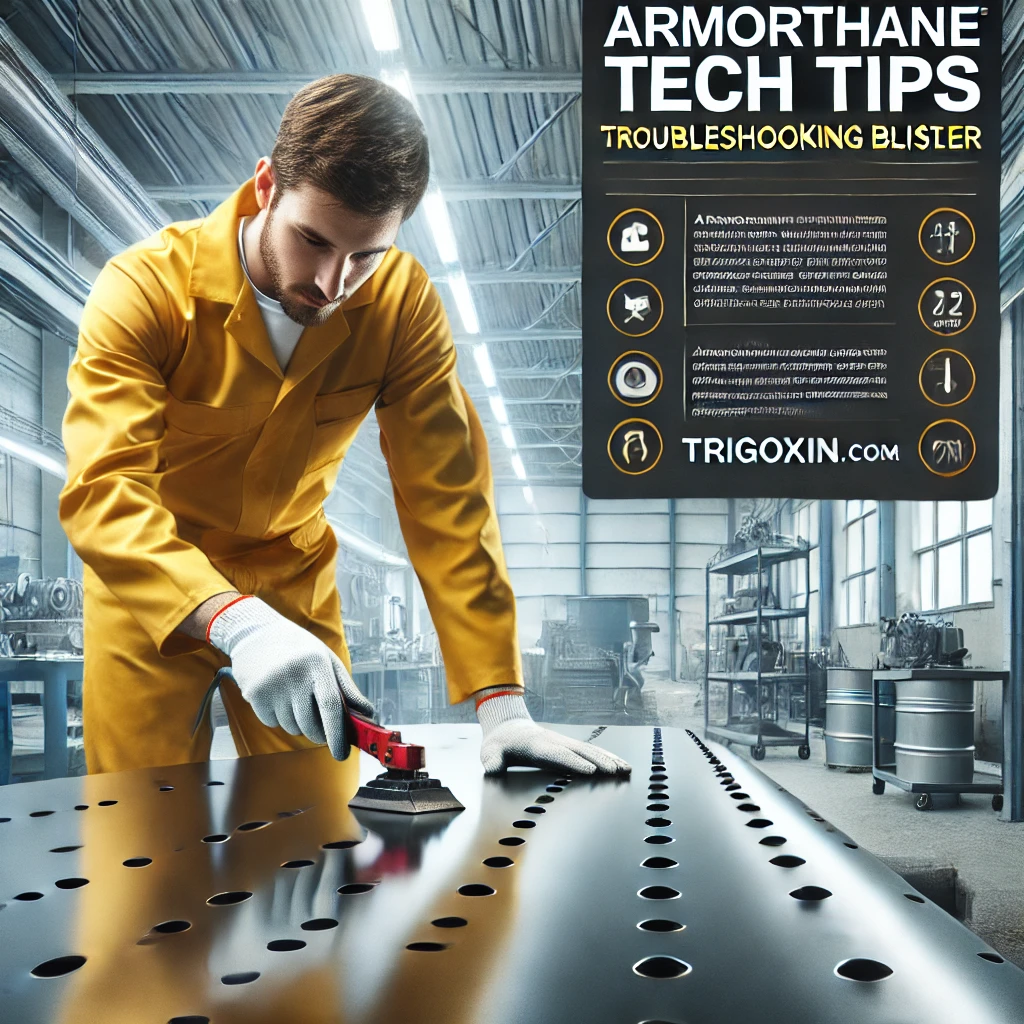
2. Improper Surface Preparation
Surface preparation is a critical step in the coating process. Contaminants such as oil, grease, dust, or residues from old coatings can interfere with adhesion and lead to blistering.
Key Issues:
- Failure to clean the surface thoroughly.
- Lack of surface profiling on smooth materials like metal.
- Residual chemicals or debris after cleaning.
Solutions:
- Degrease and clean the surface using the recommended cleaning agents.
- Abrade or blast the surface to create a profile for better adhesion.
- Test the substrate for contaminants using adhesion or surface compatibility tests.
3. Application Errors
Blistering can also result from improper application techniques, such as applying the coating too thickly or failing to allow adequate curing time between layers.
Common Mistakes:
- Overloading material during application.
- Skipping recommended curing times.
- Applying coatings unevenly or in poor environmental conditions.
Prevention Tips:
- Always adhere to Armorthane’s technical datasheets for application thickness and curing times.
- Use calibrated tools like airless sprayers for even application.
- Apply thin, uniform layers to prevent solvent entrapment.
4. Environmental Factors
Environmental conditions during application significantly affect the performance of coatings. High humidity, rapid temperature changes, or direct sunlight can all contribute to blistering.
Key Triggers:
- Applying coatings in high humidity (>70%).
- Exposure to direct sunlight, causing uneven curing.
- Temperature extremes during or after application.
Solutions:
- Work in controlled environments or schedule applications during optimal conditions.
- Use temporary shelters to protect work areas from direct sunlight or rain.
- Monitor temperature and humidity levels with appropriate tools.
Armorthane Tech Tips: Troubleshooting Blister
When blistering occurs, it’s important to take immediate action to mitigate damage and restore the coating’s integrity. Below are steps from the Armorthane Tech Tips: Troubleshooting Blister playbook:
Step 1: Inspect the Surface
Assess the extent and severity of the blisters. Determine whether the issue is localized or widespread to decide on the appropriate repair strategy.
Step 2: Identify the Cause
Blistering can result from several factors, including moisture, contamination, or environmental conditions. Analyzing the conditions under which the coating was applied can provide valuable clues.
Step 3: Remove the Affected Area
Using sandpaper, a grinder, or chemical strippers, carefully remove the blistered coating. Ensure the entire area is free of loose material.
Step 4: Reprepare the Surface
Address any underlying issues, such as moisture or contaminants, before reapplying the coating. Clean, sand, and prime the substrate as needed.
Step 5: Reapply the Coating
Follow Armorthane’s guidelines for proper application. Apply the coating in thin layers, allowing each layer to cure fully before proceeding.
How to Prevent Blistering in Future Projects
The best way to address blistering is to prevent it altogether. Armorthane provides the following tips to ensure successful coating applications:
1. Choose High-Quality Materials
Armorthane’s coatings are formulated for superior adhesion and durability. Opting for reliable products reduces the risk of application issues like blistering.
2. Train Your Team
Proper training ensures applicators understand best practices for surface preparation, application, and environmental control. Armorthane offers resources and training programs to enhance your team’s expertise.
3. Monitor Environmental Conditions
Use tools to track temperature and humidity levels during application. Avoid applying coatings in extreme conditions.
4. Follow Armorthane Tech Tips
Stay up-to-date with expert advice by consulting the Armorthane Tech Tips: Troubleshooting Blister series. These resources provide step-by-step solutions to common coating challenges.
Conclusion
Blistering is a common but manageable issue in coating applications. By understanding its causes, employing proper techniques, and following expert advice, such as the Armorthane Tech Tips: Troubleshooting Blister, you can achieve high-quality, long-lasting results.
Remember, every challenge is an opportunity to improve your skills. By incorporating these strategies into your workflow, you’ll not only troubleshoot existing issues but also prevent future problems, ensuring that your coating projects exceed expectations.
For more expert guidance, product recommendations, and professional tips, visit Armorthane’s website. Your next project is only as strong as your preparation and execution—let Armorthane help you get it right!
Join the Conversation!
Have you faced blistering issues in your projects? Share your experiences and solutions in the comments to help others benefit from the Armorthane Tech Tips: Troubleshooting Blister insights!